Inspection of high-value electronic assemblies
Home » Customer Stories » Inspection of high-value electronic assemblies
Home » Customer Stories » Inspection of high-value electronic assemblies
Industry: Semiconductor
The Challenge
Our customer, a semiconductor chip manufacturer, faced challenges with the inspection of their high-value electronic assemblies. The complexity of these assemblies made it difficult for human inspectors to identify defects or irregularities with the necessary precision, which meant that subtle defects may go unnoticed.
Additionally, the manual inspection process was time-consuming, leading to increased production costs and potential delays.
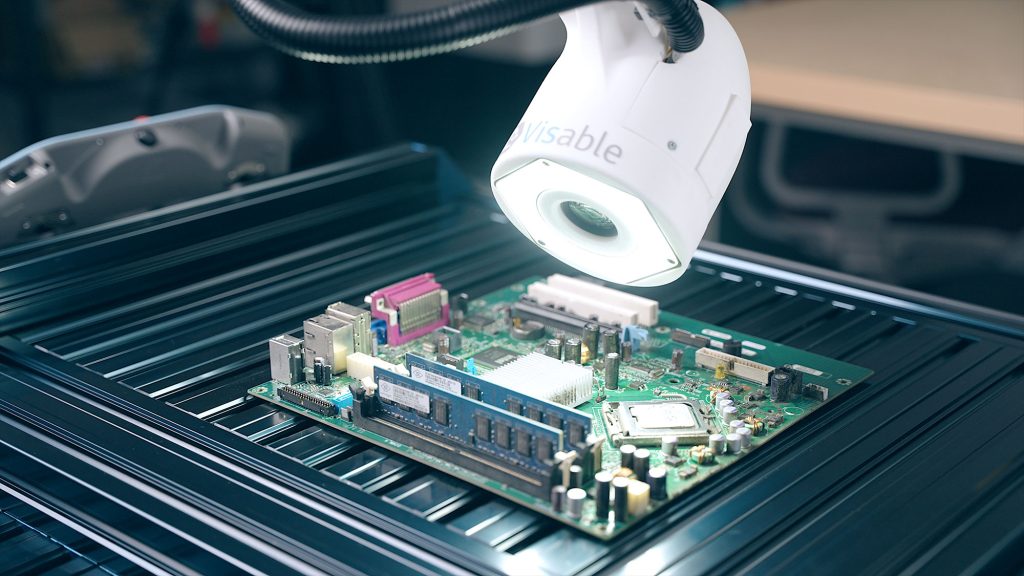
Solution
Working closely with our customer, we concluded that adoption of automated inspection technology would enhance the reliability and productivity of their processes.
We provided our Visable No-Code Robotic Vision Inspection solution to inspect production critical electronic equipment.
Visable was put through a thorough safety certification process, enabling the use of the solution without additional robot guarding and making this one of the first true collaborative robotic applications deployed at any of their sites globally.
Leveraging the plugin architecture of Visable, we were able to provide customised plugins to facilitate seamless factory integration at the customer sites.
Deploying one of Visable’s latest features, we enabled the customer to implement their own complex image processing tools via external Python integrations, allowing the customer to generate their own IP in the inspection process.
Results
The collaborative robot version of the solution achieved several significant milestones for the customer. The inspection time was significantly reduced from 30 minutes to an impressive 3 minutes, showcasing the unparalleled efficiency of Visable. It allowed our customer to enhance their competitiveness and ensure reliability of their inspection processes.