Weld Inspection
Home » Customer Stories » Weld Inspection
Home » Customer Stories » Weld Inspection
Industry: Medical Device
The Challenge
Our customer, a manufacturer of medical devices, faced significant challenges with the inspection of tiny, intricate welds in their components, where weld diameters were as small as 0.1 mm. The complexity and scale of these parts made manual inspection highly challenging and error-prone, leading to concerns about accuracy and reliability.
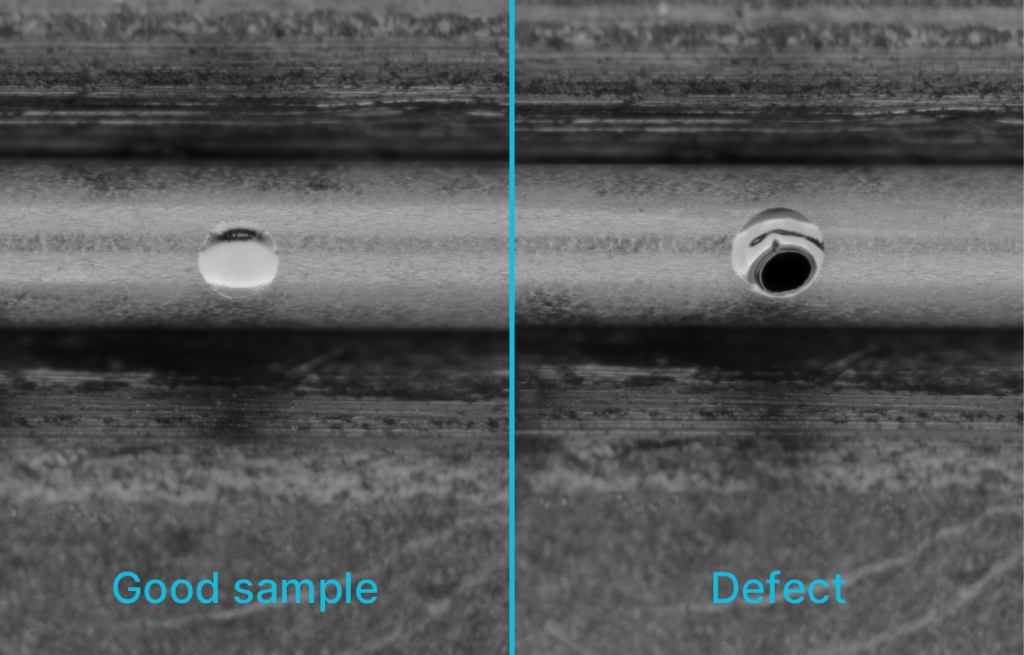
Solution
To address the challenge of inspecting tiny, intricate welds with diameters as small as 0.1 mm, we developed a custom deep learning model specifically designed for this task. By imaging 4,000 parts during the development process, the model was trained to accurately identify and assess weld quality, even at such a small scale.
The deep learning solution automated the inspection process, significantly improving both accuracy and reliability compared to manual inspection. This advanced model enabled the customer to detect even the slightest defects in the welds, ensuring consistently high-quality components and reducing the risk of product failures.
Results
As a result of implementing the deep learning model, the customer achieved an inspection accuracy of over 99.8%, significantly reducing errors and improving the overall quality of their welds.
The automated process not only enhanced consistency but also met the stringent regulatory requirements of the medical device industry. The inspection system received FDA approval, ensuring that the customer’s components adhered to the highest standards of safety and reliability, while also increasing operational efficiency and minimizing the risk of product failures.